半導体の故障解析
<事例内容>
PKGの実装前の観察画像に対し、基板実装後に内部の様子に変化が生じたため、観察画像の結果より、故障部位の「平面研磨」及び「断面研磨」を行い、原因の特定を行いました。
同モードの不良がいくつかある場合には、平面研磨・断面研磨と両方からの解析及び観察ができます。<解析結果と判断>変化した部位に空洞が発生していることから、電子部品と基板間には半田ボールで接続後、アンダーフィルを流し込み密着性を上げました。
この白い部分には「隙間」が発生したと考えられます。
超音波探傷装置によるPKG内部密着度観察
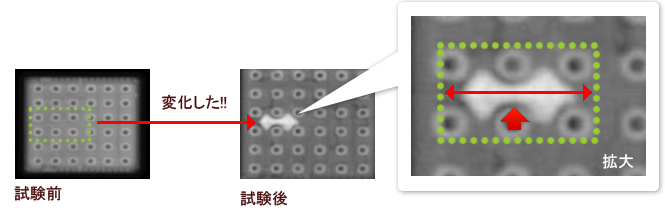
断面研磨方向
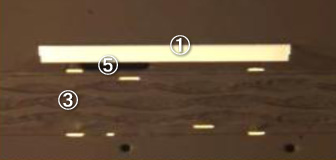
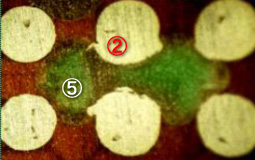
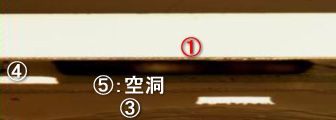
①ペレットチップ
②PKGのボール端子
③基板
④アンダーフィル
⑤故障箇所(ボイド発生)
実装信頼性接合部故障解析事例
<手順>
- 現品の観察(目視・金属顕微鏡・X線・超音波探傷観察)
→詳細な観察と外観から得られる情報の記録 - 電気的特性調査→不良項目から構造的に考えられる不良部位の特定、及び構造の理解・X線等の観察
→今回の不良は特定端子の導通不良 - 不良解析方法の決定(例として、断面研磨による故障解析事例を紹介)
このサンプルは、断面研磨で仕上げたものです。
断面研磨品 PKG全体観察

①ペレットチップ
②PKGのボール端子
③接続ポスト
④実装基板
⑤製品(電子部品)と基板の接続点
不良部位の拡大観察
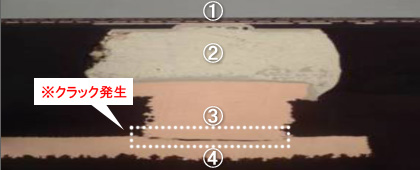
断面研磨を行い、電気的特性から絞り込んだ端子において、基板と基板ポスト部にクラックが確認。
電子部品のボール部は十分接合されている。
①ペレットチップ
②電子部品の半田ボール
③ポスト部
④実装基板配線
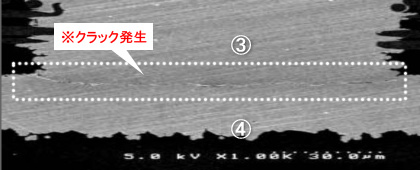
SEMで拡大観察し不良箇所を特定。
実装品の一般的な故障解析
故障解析と信頼性評価
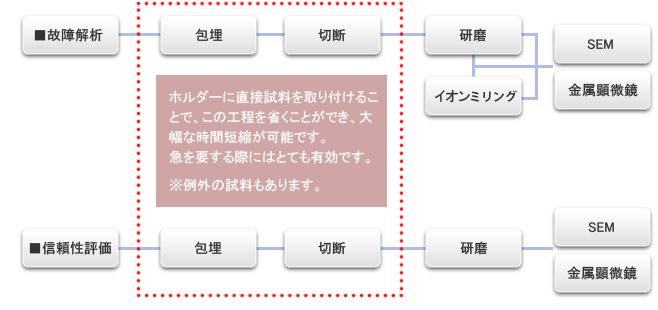
故障解析の事例
〜ボンディングの接合不良による故障解析の研磨手順
■使用試料ホルダ:一軸傾斜ホルダ
■研磨ポイント:電気的特性で絞り込んだ部位の配列断面を正確に露出させる。
■不良内容は、端子のオープン(未接合)不良
<手順>
- 現品の観察
→詳細な観察と外観から得られる情報の記録 - 電気的特性調査
→不良項目から構造的に考えられる不良部位の特定及び構造の理解・X線等の観察 - 不良解析方法の決定(例として、断面研磨を紹介)
→研磨進行と構造的部位に着目しながら研磨レシピを変更
故障解析の研磨手順 1

絞り込んだ端子側から研磨を開始する。
→まずは外部端子からの接続線の断面が点状に現れる。
故障解析の研磨手順 2

最初にペレットチップが搭載されているリードフレームの側面が顔をだす。
故障解析の研磨手順 3

更に研磨が進むとチップ側面が顔をだす。
左右の均一性を確認。
故障解析の研磨手順 4

その後、ボンディング側面が顔をだす。
左右の均一性を確認、観察したい端子に着目する。
故障解析の研磨手順 5
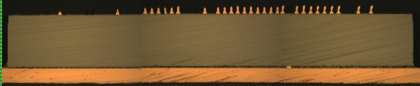
バフ研磨を行い、ボンディング表面と、チップとの接続面の出来栄えを確認し、
高倍率のSEM等で最終観察を行い、不良箇所が電気的特性結果と一致する事を確認する。
故障解析の研磨手順 6
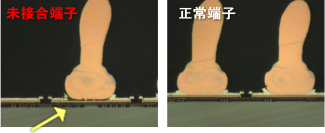
不良の端子を良品端子と比較し構造的違いを観察する。
→不良端子:Bd下に隙間がある
→良品端子:Bd下は密着している
故障解析の研磨手順 7

SEMで拡大観察し不良箇所を特定する。
コメントを投稿するにはログインしてください。