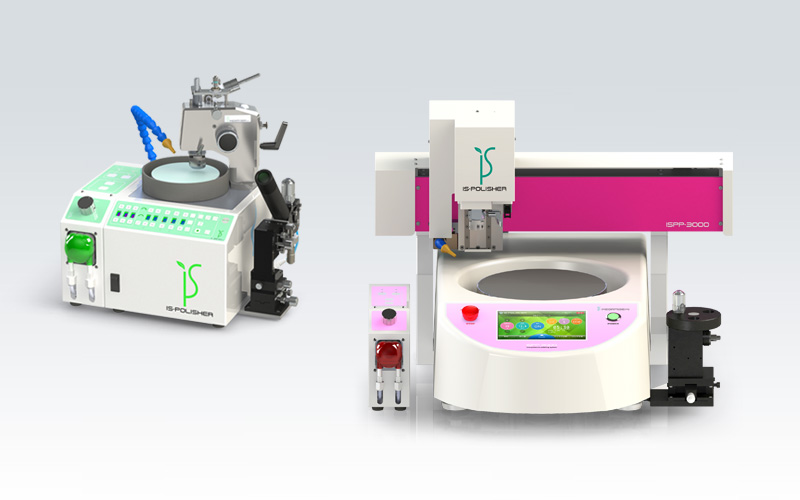
これまでとの違い
IS-POLISHERは、ホルダ方式と荷重調整機構の採用により低負荷で研磨ができる唯一の試料研磨機です。
試料ホルダと荷重調整機
包埋せずに直接試料をホルダで保持することで、研磨面積を小さくすることができ、荷重調整機構による低い荷重の研磨を実現しました。
これにより、試料にかかる負荷を減らし、組織を壊さずに研磨することができ、これまで難しいとされてきたEBSD像や菊池パターンの観察が可能となりました。
これがIS-POLISHERの低負荷・低荷重研磨です。
ホルダを装着するスイングアーム機構
- 1μm単位で削り過ぎを防止できます。
- 微細、微小な試料の仕上げを可能にする最低25gの荷重が設定できます。
- 試料を外すことなく観察できる顕微鏡は、再現性と作業効率を向上させます。
軟らかい金属、半導体や電子部品などの微小部品、これらの試料に共通して、
観察したい面が出せないというお客様の課題がありました。
試料に負荷を与えない研磨
これまでの研磨
これまでの研磨では、試料に大きな荷重をかけてしまっています。
これにより試料面に大きな負荷がかかり、加工変質を起こしてしまい、結果的に組織に歪みを与えてしまうという点に着目し、この課題を解決する研磨機の開発に着手しました。
低負荷で研磨を行うウェイトキャンセラ機構
低い荷重で試料に負荷を与えずに研磨ができる機構の「ウェイトキャンセラ」を開発しました。
ウェイトキャンセラ機構により、試料に負荷を与えずに研磨ができるようになり、加工変質を最小限に抑えることが可能となりました。
低負荷・低荷重
ウェイトキャンセラ機構を使った低負荷・低荷重研磨によって、難易度が高いとされてきた試料研磨が可能になりました。
Ⅰ. 軟らかい金属のEBSD像が撮れる面の作製
Ⅱ. 硬さの違う金属同士の複合材料
Ⅲ. 半導体、電子部品などの微小微細な部品
Ⅳ. 炭素繊維強化樹脂など割れや欠けを起こしやすい材質
Ⅴ. 積層フィルム、塗料、ポリマーのような材料
Ⅵ. 岩石の薄片化
このように、さまざまな分野、業界で課題を抱える多くのお客様に導入いただいております。
Ⅰ. EBSD (Electron Backscattered Diffraction:電子後方散乱回析)
結晶性の材料に電子線を照射すると、回折は試料表面の数10nmの領域から反射電子を発生します。
このため十分に細い電子線を照射すれば100nm程度の分解能の情報を得ることができます。
ただし、研磨による試料の仕上がり具合いで大きく影響されます。
特に、試料表面に研磨時の機械的応力による加工変質層があると、正確に評価を行う事が難しくなります。
軟らかい金属ではその影響がさらに大きくなります。
加工変質層を減らすためは研磨時の試料負荷(荷重)を極力減らすことが重要です。
ウエイトキャンセラ機構は試料にかかる荷重を管理でき、試料への負荷が少ない研磨を可能にしました。
これによりEBSDによるきれいな結晶方位解析が可能となりました。
EBSD応用例:熱処理温度を変えた場合の結晶方位像の違い
下図は1000℃と1200℃で溶体化処理したSUS304を、IS-POLISHERを使って通常研磨とコロイダルシリカ(Si02)を用いて研磨した試料表面を、EBSDで観察したIPF(方位マッピング)像です。
軟らかい金属のEBSD像
半導体のアルミワイヤボンディング部
信頼性にかかわるさまざまなことがEBSD像によってわかる
Ⅱ. 硬さの違う金属同士の複合材料
硬さの違う金属同士の研磨は、硬い材質に合わせた研磨レシピを組みます。軟らかい材質にレシピを合わせても、硬い材質は研磨できません。
弊社ではできるだけ固定砥粒を使った研磨レシピを推奨しています。
遊離砥粒の場合、砥粒が研磨面で遊びまわり、特に硬さの違う領域に砥粒が集まり、境界面に段差が生じてしまいます。ここに段差が生じることで、平坦な研磨面が得られません。
他社研磨機で実現できないのは樹脂包埋が主流であり、バフ工程で遊離砥部粒を使い、長い時間研磨作製を行うことで、材質の異なる試料作製がなかなかうまくいかないようです。
IS-POLISHERのレシピは固定砥粒のため、砥粒が遊びまわらないので、段差が生じず、理想とする研磨面を得ることができます。
ISーPOLISHERの機能と、理想的研磨レシピの選択により、目的とする試料が可能になります。
Ⅲ. 半導体、電子部品などの微小微細な部品
従来(他社研磨機は)小さな試料を1インチの包埋ケースに埋め込んで研磨することで、研磨面積が大きくなり、過大な荷重をかけて研磨することになります。
また、面積が大きい分、研磨時間も長くなります。
過大な荷重をかけることで、樹脂包埋してあったとしても、加工歪は試料内部に伝わってしまいます。さらに、部品が小さいことから、削り過ぎの問題が発生します。
部品そのものを直接ホルダに保持することで、研磨面積を小さくでき、低荷重で研磨ができることから、試料にストレスを与えることなく、正確な研磨面を得ることができます。
また研磨量調整機構を使って、削り過ぎを防止することが可能です。
Ⅳ. 炭素繊維強化樹脂など割れや欠けを起こしやすい材質
従来(他社研磨機)は、樹脂中に含まれているもろい材料を、1インチの包埋ケースに埋め込んで研磨をしています。
この場合、研磨面積が大きくなり過大な荷重をかけなければならず、もろいガラス等が機械的ストレスを受け、試料が欠けやすくなります。
もろい材料で構成されている試料は、IS-POLISHERの低荷重研磨により、試料がストレスを受けることなく、欠け、割れを発生させずにきれいな研磨面を得ることができます。
Ⅴ. 積層フィルム、塗料、ポリマーのような材料
従来は1インチの包埋ケースに埋め込み研磨をしています。そのため、研磨面積が大きくなり、研磨時間がかかり、包埋した樹脂の影響によりSEM等の観察時にチャージアップし良い分析ができないことがあります。
また、包埋した樹脂が試料内に入り込み、正しい分析ができないという声もあります。できるだけ研磨面積を小さくするため、簡易包埋方法を選択しています。
簡易包埋は短時間で研磨面の固定ができ、少ない研磨面積で試料作製が可能になります。
Ⅵ. 岩石の薄片化
岩石を薄くして、光学系の顕微鏡で組織、混合物等の観察を行い、岩石の中に含まれる鉱物の種類を見極める。
厚さ30μmの岩石薄片を作れる職人もいますが、岩石の薄片研磨は、基本「手研磨」が主流となっていますが、手研磨は疲れる、薄片研磨が難しい(作業者の感覚に頼るので人によるバラつきが大きい)という課題があります。
ISーPOLISHERの研磨量調整機構をつかい、削り量を設定すれば、希望の指定厚の試料研磨が自動でできます。
菊池パターンの発生
この機能の開発によって、これまで研磨では困難とされてきた菊池パターンの発生を容易に行うことができるようになりました。
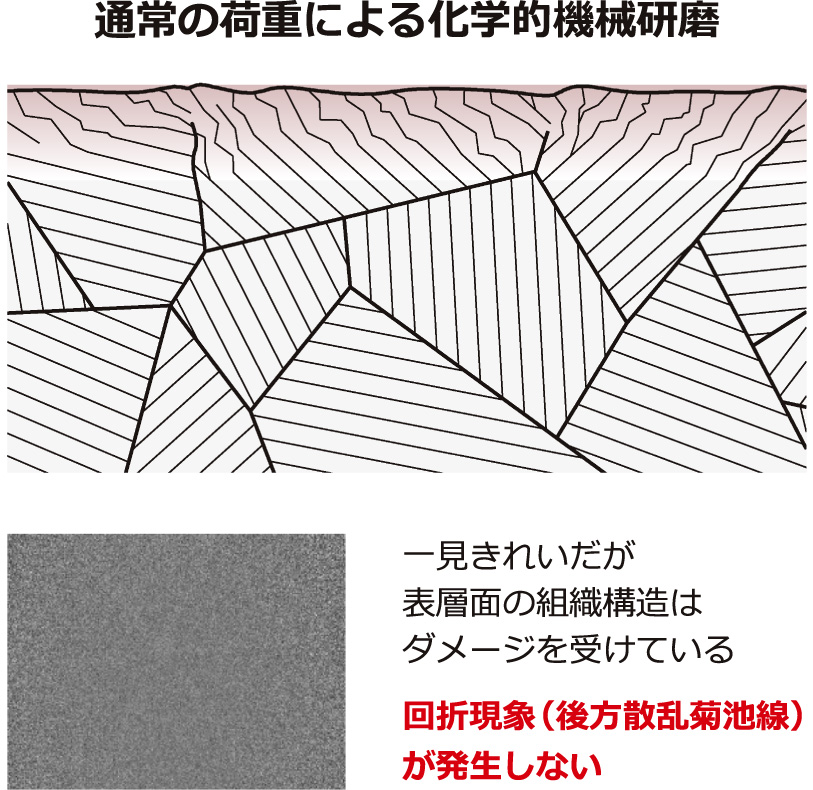
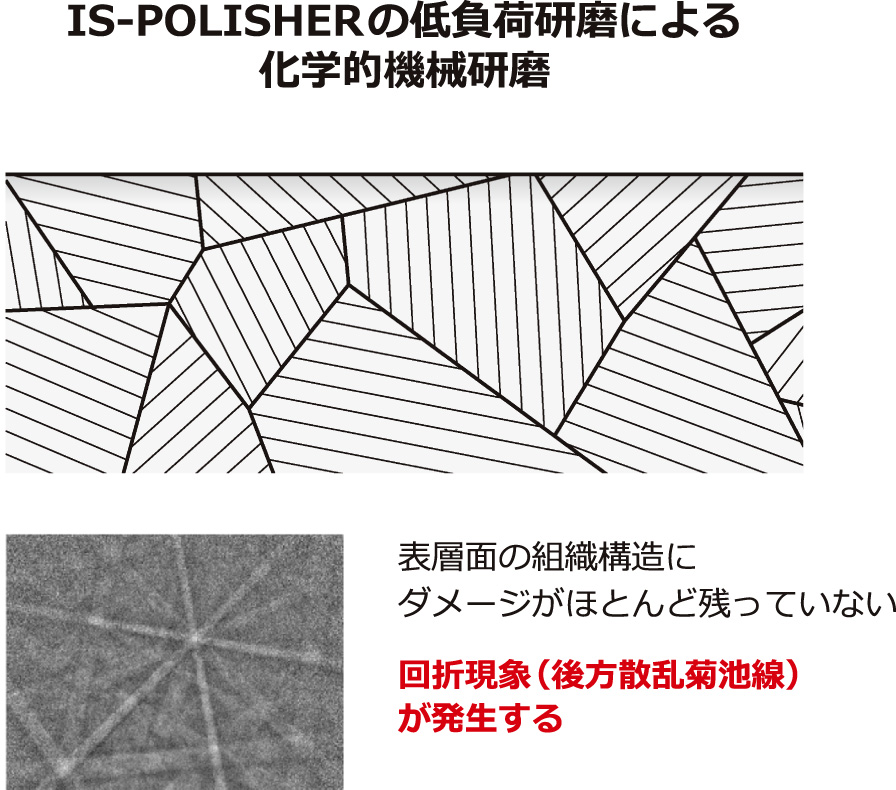
低負荷に必要な試料ホルダ
低い荷重で研磨を行うためには、試料の面積を最小限にする必要がありました。
それを実現するために、試料を直接つかむホルダを開発しました。
コメントを投稿するにはログインしてください。